OMEGA DIECAST PISTONS - STD 1275

Description
The MED/Omega die cast pistons are now even lighter than the original and are ideal for any A-Series engine from fast road to full race.
By special request we now produce a standard bore size piston for the large bore engines, so 1275, 1071 and 970. These are ideal for re-linered blocks or where a re-bore is not required, and have proved particularly popular with classic restorers.
Supplied as a set of four with ring pack, which is also available separately if you require spares.
Click the Extra Info and Technical Downloads tabs for more detail.
- 6.5cc dish
- Standard 20.6mm (13/16") press-fit gudgeon pins
- Optional short pins and clips for fully-floating little ends

Additional Information
Diecast vs forged
Diecasting is a more affordable construction method compared to forging. In general, alloy castings are not as strong as forgings, so the diecast pistons tend to weigh more to retain high strength.
However, Omega cast pistons have been used very successfully for decades in all manner of A-Series engines, from daily drivers to competition cars. Do not confuse these pistons for standard factory-spec cast items - they are still a very high performance piston, CNC machined to the same exacting standards as the forged Omegas.
As a general rule, opt for forged pistons if you wish to exceed a static compression ratio of 11:1, have a very high performance engine or wish to run high boost levels on a forced induction setup.
Running clearances
For a mild road engine build we would recommend a skirt clearance of 0.0025", increasing to 0.003" for higher performance usage. However, this is only a guide - different engine builders will have their own preferences.
The recommended ring gap is 0.010"-0.012".
Gudgeon pin size
All diecast Omega pistons utilise a standard diameter 20.6mm (13/16") gudgeon pin. We can supply shorter pins and retaining clips if you wish to convert to a floating setup.
Our forged pistons mostly use a smaller, lighter 18mm diameter pin.
Floating pins
'Fully floating' refers to the gudgeon pin fitment to the conrod little end, where the little end is enlarged and bushed by a machine shop. Rather than being fixed in position, the gudgeon pin can still rotate freely in the bushed little end.
The fully-floating setup is preferred by race engine builders for ease of assembly/disassembly. There is also less chance of damaging the pistons on insertion.
The downside is that we do not keep little end bushes for these standard 20.6mm (13/16") pins, so these will need to be custom made to suit.
Fixed pins are the most popular choice with diecast pistons.
Conrod choice
These are designed to be press-fitted onto standard production conrods for the 1275 engine. That includes Cooper S, Midget, 1275 GT and all A+ engines, plus SPi and MPi.
Piston size
A larger capacity will produce more power for any given engine spec, so when maximum performance is the goal, offset boring to 1380cc (73.5mm) is the way to go.
However, with the increasing cost of core 1275 blocks, we generally recommend boring to the next oversize for longevity. Your machine shop will be able to make the appropriate measurements and advise further on this.
We do not recommend a larger bore than 73.5mm for reliability.
Crown type
Our diecast range have several options on crown type - flat top, small dish and large dish. All pistons start with a flat top and are machined accordingly.
The crown top needs to be taken into account when calculating compression ratio.
Custom pistons
Unfortunately we are not able to produce custom one-off pistons, due to the initial drawing and tooling costs involved. However we do stock a very wide range of pistons to suit the vast majority of 1275-based engine builds.
Production process
This process requires the melting of a special high-silicon alloy in an electric furnace with extremely closely controlled temperature. The molten alloy is then poured into a multi-piece die, producing a very accurately shaped piston casting.
The casting die is manufactured so that when the metal has solidified, the various pieces of the die can be extracted one by one. This means that undercuts and reliefs can be produced in the casting to reduce the piston weight.
Related Products
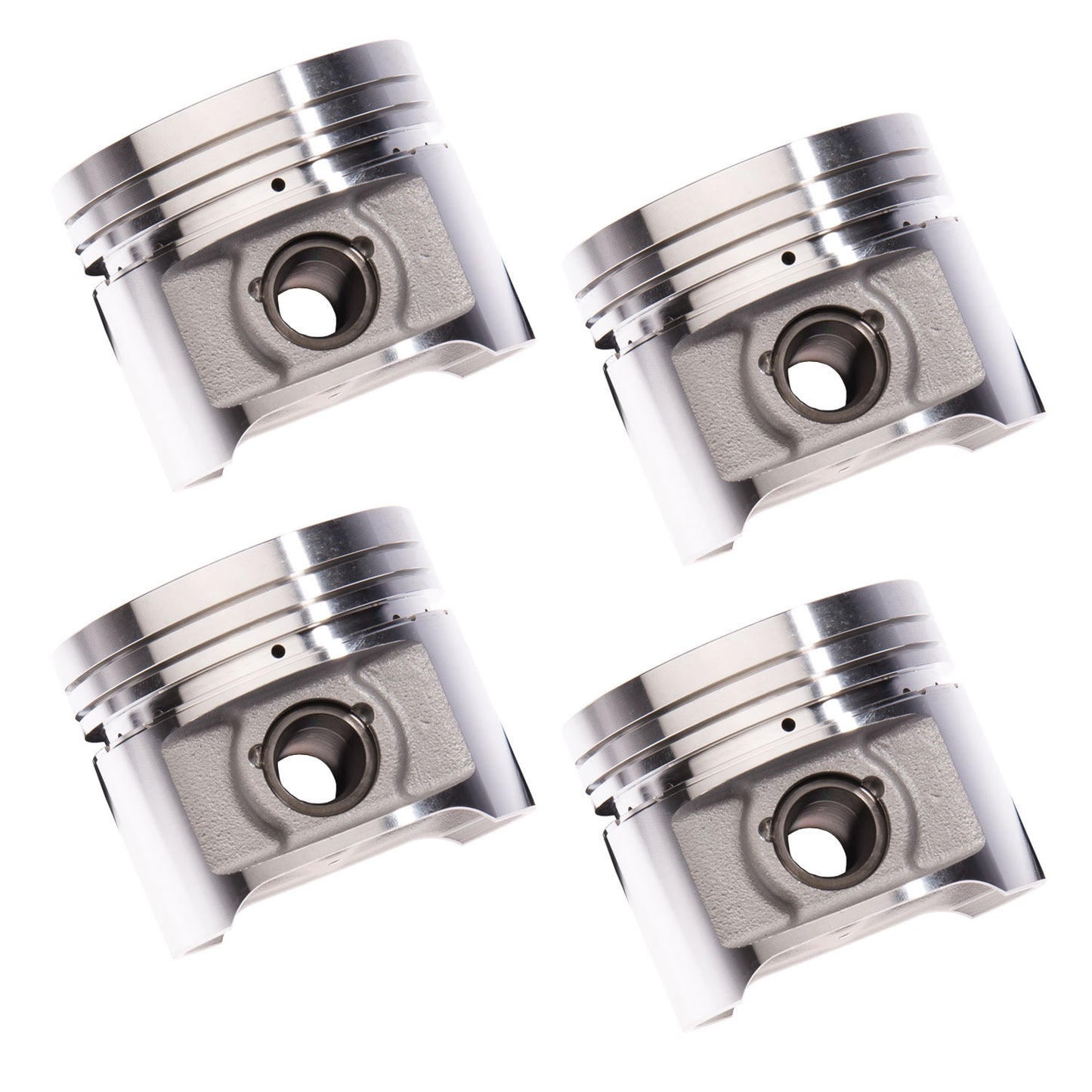